REDUCE INSPECTION TIME BY UP TO 90%
In most factories, compressed air systems are one of the largest electricity cost centers. That’s why it’s important to detect compressed air leaks and equipment inefficiencies as early as possible – and fix them immediately. But finding air leaks isn’t easy to do using traditional inspection methods, such as soap bubble testing, which take significant time.
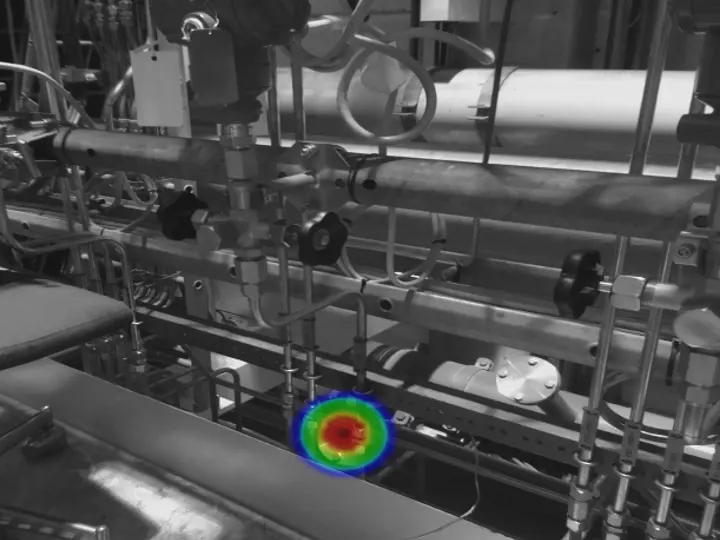
The FLIR Si124 is ideal for pinpointing leaks in complicated, difficult-to-access locations.
Most leaks create turbulence which in turn creates ultrasonic noise. An acoustic imaging camera, such as the FLIR Si124, pinpoints the source of that noise and overlays that “hot spot” onto a visual camera picture in real time. By imaging the noise source, we can improve ultrasound inspection time by approximately 90 percent. Inspectors can also quickly scan large areas with the camera from a safe distance without touching machinery or shutting down the line. The FLIR Si124 sees through background noise commonly found in industrial environments to produce precise imagery. By listening, recognizing, analyzing ultrasonic sounds, and ultimately understanding what different sounds mean, an acoustic imager allows operators to instantly and accurately pinpoint the source of an air leak.
Adopting acoustic imaging as part of a predictive maintenance routine, professionals can identify issues fast, cut excess costs, and keep manufacturing operations going.